Polyurethane Solutions for Highest Demands
Flexible, durable and versatile - for individual requirements
Polyurethan - Quality since 1965
Welcome to Lutze - Kunststofftechnik
For over 60 years, our Polyurethane Solutions division has stood for innovation, quality and tailor-made product solutions in a wide range of industries.
Under the brand name LUWITAN®, we develop high-quality polyurethane molded parts and coatings that impress with their durability, wear resistance and a wide range of applications.
Our strengths:
- Quality: We rely on careful raw material selection and precise planning to meet the highest demands.
- Diversity: Our extensive portfolio of LUWITAN® qualities is continuously being developed to meet your requirements.
- Flexibility: Thanks to optimized production processes, we offer solutions for both small series and large-scale production.
Discover how our products can make the difference - for your applications and your industry.
LUWITAN® - quality that moves.
Products and solutions
LUWITAN® polyurethane elastomers
Our LUWITAN® products set standards in quality, durability and versatility. For decades, customers from a wide range of industries have trusted our innovative polyurethane solutions - from molded parts to specialized coatings.
Our portfolio:
- Molded parts:
Precisely manufactured polyurethane parts that are characterized by high resilience and wear resistance. We offer open casting, rotational casting, vacuum casting or mold casting. Ideal for demanding industrial applications. - Coatings:
High-quality polyurethane coatings that optimally protect machines and components and extend their service life. - Individual solutions:
Together with you, we develop tailor-made products that are precisely tailored to your requirements. - Mold making - flexibility in every format:
No matter what format your drawings are in - we can read all formats and work with the latest CAD technology to create precise and efficient molds. Trust in our expertise in mold making, regardless of the type of file.
Why LUWITAN®?
- Wear-resistant and durable: Maximum durability even under extreme conditions.
- Versatile: A wide range of applications for different industries, from mechanical engineering to transportation.
- Flexible in production: Whether small or large series - we offer you the right solution.
Discover how our polyurethane elastomers can optimize your processes. Contact us to find out more about our products or to receive an individual offer.
LUWITAN® - your solution for tomorrow, today.
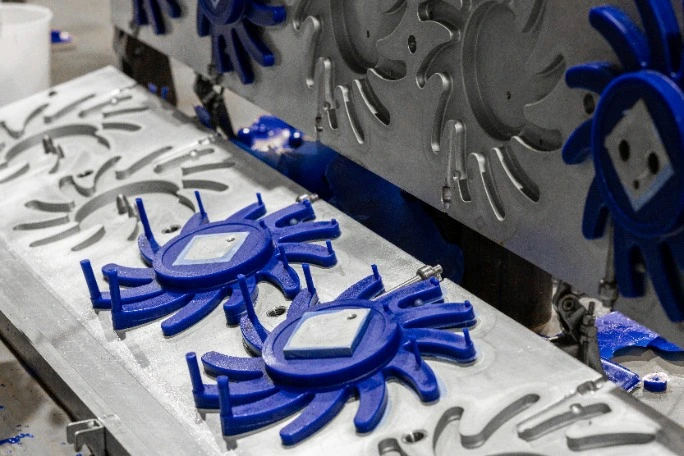
Do you know LUWITAN®?
LUWITAN® – a name that many of our customers have long since integrated into their everyday work. But what is actually behind this name?
LUWITAN® is Lutze Group's protected brand name for high-quality polyurethane solutions that were specially developed for molded parts and wear-resistant coatings. The history of LUWITAN® began in 1965, when Heinz Lutze Senior and engineer M. Winkler were looking for a solution for coating conveyor belt rollers with polyurethane. The result: an innovative system that quickly became a success.
The name LUWITAN® reflects this collaboration:
- "LU" stands for Lutze,
- "WI" for Winkler,
- and "TAN" refers to the suffix of "polyurethane".
Flexibility and innovation
LUWITAN® stands for tailor-made polyurethane solutions based on a variety of proven recipes. Thanks to our protected brand and our broad raw material network, we are not tied to individual suppliers. This enables us to react flexibly to market changes and provide the optimal solution for every requirement - with consistently high quality and performance.
LUWITAN® – proven tailor-made polyurethane solutions.
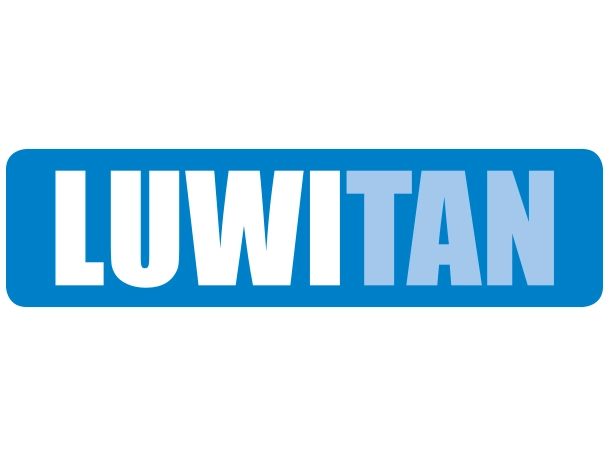
LUWITAN® Polyurethane has many high-quality physical properties
Some examples and advantages

Cut resistance
Excellent cut and notch resistance.

Abrasion resistance
Exceptional resistance to mechanical wear.

Chemical resistance
Provides resistance to a wide range of chemical substances.

Impact resistance
Protects the material from impacts and preserves its integrity.

Temperature resistance
Withstands extreme temperatures in both cold and hot environments.

Hydrolysis resistance
Resistant to degradation by water, which is important for applications in damp or wet environments.

Flex-fatigue resistance
Resists fatigue from repeated bending and stretching, which is essential for dynamic applications.

Tear propagation resistance
Promotes longevity by preventing the propagation of tears.

Elasticity
Allows flexibility and return to original shape after deformation.

Weather resistance
Effectively resists environmental influences such as UV rays and moisture.

Food-safe
Suitable for use in the food sector with direct contact.

Microbe resistance
Resists degradation by microorganisms making it ideal for medical and hygienic applications.

Hysteresis
Optimizes efficiency by minimizing energy loss in dynamic applications.

...
Your partner for polyurethane solutions and molding
Welcome to your specialist for polyurethane molded parts and LUWITAN® coatings! We use the latest manufacturing processes to meet your individual requirements - from the smallest components weighing just a few grams to series products weighing several hundred kilograms.
Our brand product LUWITAN® stands for high-quality hot-cast polyurethanes with hardnesses from 45 Shore A to 72 Shore D, and in special cases even from 30 Shore A to 80 Shore D.
Discover our wide range of services in plastics technology and find out more about our innovative solutions for a wide variety of applications. We are at your side as a competent partner!
Molded parts made of LUWITAN®
Precision and quality
LUWITAN® stands for customized polyurethane solutions based on a variety of proven recipes. Thanks to our protected brand and our broad raw material network, we are not tied to individual suppliers. This allows us to respond flexibly to market changes and provide the optimal solution for every requirement – with consistently high quality and performance.
We are at your side as a partner right from the planning phase of your components - cost-oriented and quality-conscious. On request, we can also create customer-specific molds to optimally implement your individual requirements.
LUWITAN® - Trust in our know-how for precise and economical results.
Coatings with LUWITAN®
Tailor-made solutions for your requirements
More than half of the components we manufacture from LUWITAN® are coatings - proof of the versatility and quality of this technology. Our main focus is always on the optimal bond between LUWITAN® and the coating carrier (core). Through intensive laboratory tests, close cooperation with our customers and our own series of tests, we have continuously perfected our coating technology. Thanks to these developments, we can now coat not only classic metallic materials, but also materials such as wood, plastics or rubber.
Flexibility in core provision
You can provide us with the coating carriers or, if you wish, we can take over the production or procurement of the cores according to your drawings and specifications.
Diverse coating processes
To coat your components with LUWITAN®, we use various processes that are individually tailored to your requirements:
- Open or closed molding processes: For precise and uniform results.
- Spin coating: Particularly suitable for coating pipes and containers.
Rely on the latest coating technology that offers you maximum flexibility and quality. Together we will find the perfect solution for your application.
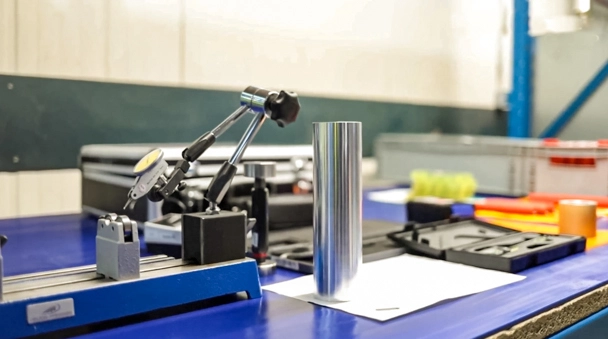
Our quality promise
Precision and reliability in every step
Quality is our top priority. That is why we ensure that all relevant processing times and process steps are strictly adhered to when processing LUWITAN®. This is the only way we can ensure that every component meets the highest standards.
Precise adherence to pot life
The pot life - the period in which the material must be introduced into the mold - varies between two and ten minutes depending on the recipe. It begins when the components come into contact and ends when the setting process starts. To ensure the best quality, the casting takes place directly from the machine's mixing head into the mold.
Exact process times for optimal results
Depending on the component, geometry and selected LUWITAN® quality, the demolding process takes a few minutes to several hours. After demolding, the PU components are reworked in a precisely coordinated tempering process. Different times and cycles are adhered to, depending on the respective recipe. In addition, the physical properties of the cast parts can be further improved by storing them at room temperature for 14 days.
Continuous quality control
Our production is constantly checked for visual defects and hardness fluctuations. If there are any deviations, we react immediately with targeted measures. In addition, we produce test plates of each recipe every day, which are archived to enable subsequent checking of the physical properties of a production batch.
With our quality promise, we guarantee you LUWITAN® products that meet the highest requirements - reliably and precisely manufactured.
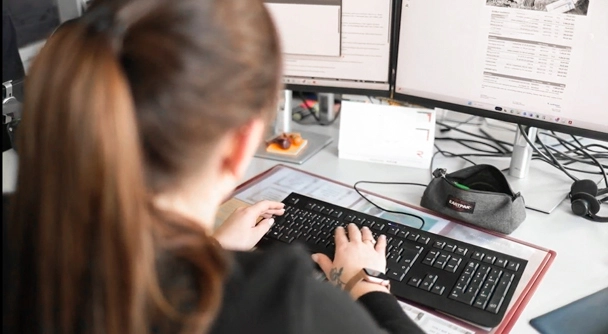
Certified according to DIN EN ISO 9001 | Lutze Kunststofftechnik GmbH & Co KG
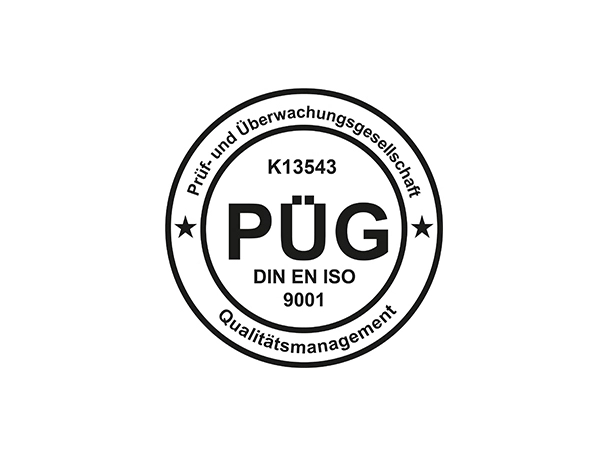
Do you have any questions about polyurethane solutions?
Contact us for more info or with a specific request