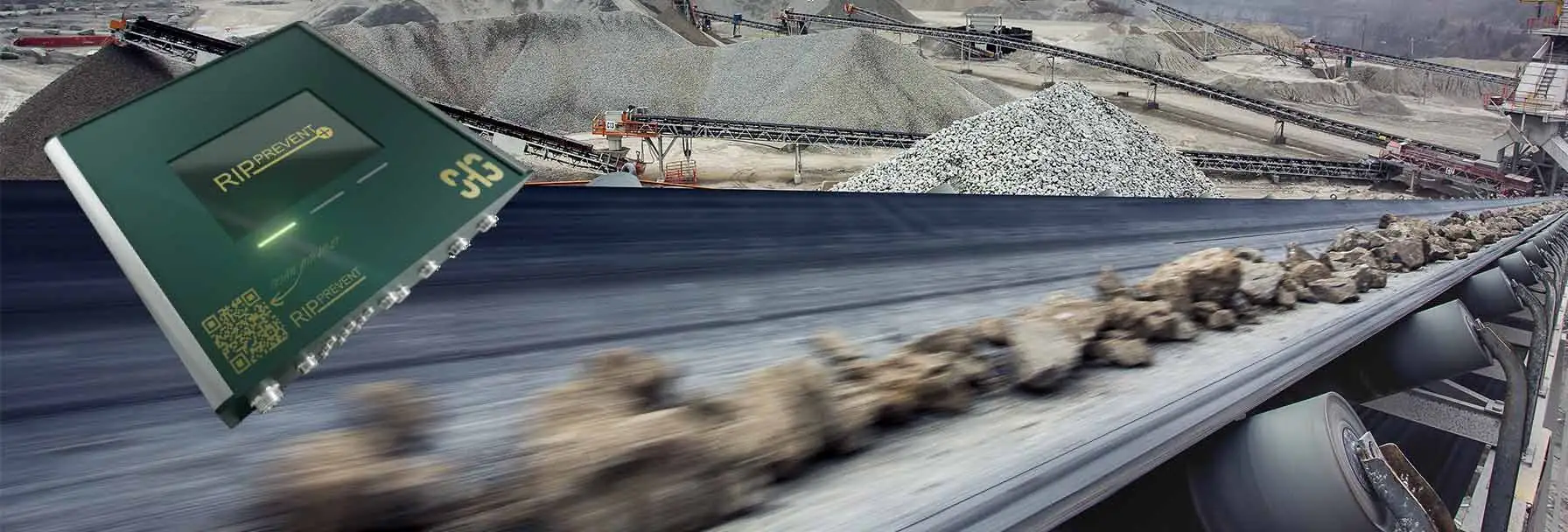
Conveyor belt monitoring
Your way towards preventive maintenance
Conveyor belt monitoring has undergone a significant transformation with the integration of AI-based predictive analytics. This powerful combination is revolutionizing industries that rely on conveyor systems by enhancing safety, efficiency, and productivity while reducing operational costs.
The traditional approach to conveyor belt monitoring often involved manual inspections and scheduled maintenance, leaving room for unexpected breakdowns and inefficiencies. The SHG Rip Prevent+ system and its AI-based predictive analytics continuously collect data from the conveyor system. Machine learning algorithms then analyze this data to predict maintenance needs and potential issues, providing real-time insights into the system's health. This proactive approach to maintenance helps avoid costly downtime, improves safety, and extends the lifespan of conveyor components.
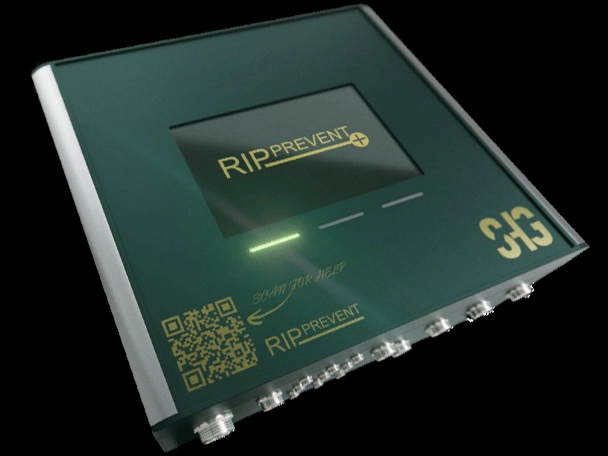
Monitoring your conveyor belts has a multitude of advantages
Enhancing safety and efficiency
Conveyor belt systems are the veins of many industries, facilitating the seamless movement of materials and products. However, their efficient operation and maintenance can be a complex challenge. Conveyor belt monitoring, coupled with AI-based predictive analytics, is transforming the way these systems are managed. It enhances both safety and efficiency, revolutionizing how industries handle their materials.
Discover from these images what functions RIP Prevent+ has inside its intelligent box.
"The system is extremely easy to install on existing conveyor systems without modifications and, in addition to rip monitoring, offers other useful features such as the belt scale function. The belt scale function has been working with a deviation of <1% since installation and does not require any calibration or maintenance during operation. During the test phase, 2 events were already detected with RipPrevent+, thus preventing significant damage and downtime."
See what RIP Prevent+ can mean to you
A more sustainable and efficient future for your conveyor belt systems
In conclusion, conveyor belt monitoring, combined with AI-based predictive analytics, offers a transformative solution for industries that rely on conveyor systems. It provides a comprehensive view of system health, improves safety, and significantly reduces downtime and maintenance costs. By harnessing the power of AI, companies can optimize their operations and make informed decisions, ensuring a more sustainable and efficient future for conveyor belt systems.
Contact us for your customised solution for efficient conveyor technology.
Find out more about the conveyor belt monitoring system
Don't wait for costly breakdowns or inefficient processes!
Reach out now to schedule a demonstration and learn how this conveyor belt monitoring technology can help you.